Understanding Bolts in the Hardware Industry: Material, Surface, and Tensile Strength
Understanding Bolts in the Hardware Industry: Material, Surface, and Tensile Strength
In the world of hardware, bolts are indispensable components that hold structures together. Whether in construction, automotive, or machinery, the quality and performance of bolts are critical to the integrity of the final product. This blog will delve into the key aspects of bolts—material, surface treatment, and tensile strength—while incorporating industry terminology and addressing market demands. By the end, you’ll have a comprehensive understanding of what makes a high-quality bolt and why it matters in today’s market.
1. Material: The Foundation of Bolt Performance
The material of a bolt determines its strength, durability, and suitability for specific applications. Common materials used in bolt manufacturing include:
1. Carbon Steel: The most widely used material due to its affordability and decent strength. Grades like Grade 2, Grade 5, and Grade 8 are popular in the U.S., with Grade 8 being the strongest.
2. Stainless Steel: Known for its corrosion resistance, stainless steel bolts (e.g., 304 and 316) are ideal for environments exposed to moisture or chemicals.
3 . Alloy Steel: Bolts from alloy steel, such as AISI 4140, offer high tensile strength and are often used in heavy-duty applications.
4 . Titanium: Lightweight and highly resistant to corrosion, titanium bolts are used in aerospace and high-performance industries.
5. Brass and Aluminum: These materials are chosen for their non-magnetic properties and aesthetic appeal, often used in electrical and decorative applications.
Market Insight: With the rise of sustainable manufacturing, there’s a growing demand for eco-friendly materials and processes. Recycled steel and low-carbon alloys are gaining traction, aligning with global environmental regulations.
2. Surface Treatment: Enhancing Durability and Aesthetics
Surface treatment is crucial for improving a bolt’s resistance to corrosion, wear, and fatigue. It also enhances the bolt’s appearance, which can be important in visible applications. Common surface treatments include:
1. Zinc Plating: A cost-effective method that provides moderate corrosion resistance. Hot-dip galvanizing offers a thicker coating for harsher environments.
2. Dacromet Coating: A zinc-aluminum flake coating that provides excellent corrosion resistance without hydrogen embrittlement.
3. Phosphating: This treatment improves adhesion for paints and coatings while offering some corrosion resistance.
4. Black Oxide: Aesthetic and mildly corrosion-resistant, black oxide is often used in automotive and machinery applications.
5. Chrome and Nickel Plating: These finishes provide a polished look and superior corrosion resistance, making them ideal for decorative and high-performance applications.
Market Insight: As industries like automotive and construction demand longer-lasting components, advanced coatings like geometry and nanocoatings are becoming more popular. These treatments offer enhanced protection without compromising the bolt’s mechanical properties.
3. Tensile Strength: The Measure of Reliability
Tensile strength is the maximum stress a bolt can withstand while being stretched or pulled before breaking. It’s a critical factor in determining a bolt’s load-bearing capacity. Tensile strength is often indicated by property classes (e.g., 8.8, 10.9, or 12.9), where the first number represents the ultimate tensile strength in MPa, and the second number indicates the yield strength ratio.
1. Low-Strength Bolts: Used in light-duty applications, such as furniture assembly.
2. Medium-Strength Bolts: Suitable for general construction and machinery.
3 . High-Strength Bolts: Essential for critical applications like bridges, skyscrapers, and heavy machinery.
Market Insight: The demand for high-strength bolts is rising, driven by infrastructure development and the need for lightweight yet durable components in industries like aerospace and renewable energy. Manufacturers are investing in advanced metallurgy and precision engineering to meet these demands.
Conclusion: Meeting Market Demands with Quality Bolts
In the competitive hardware industry, understanding the nuances of bolt materials, surface treatments, and tensile strength is essential for delivering products that meet market demands. Whether it’s the corrosion resistance required for marine applications or the high tensile strength needed for structural integrity, each aspect plays a vital role in the bolt’s performance.
As industries evolve, so do the requirements for bolts. Manufacturers must stay ahead by adopting innovative materials, advanced coatings, and precision engineering techniques. By doing so, they can ensure their products not only meet but exceed the expectations of a dynamic and demanding market.
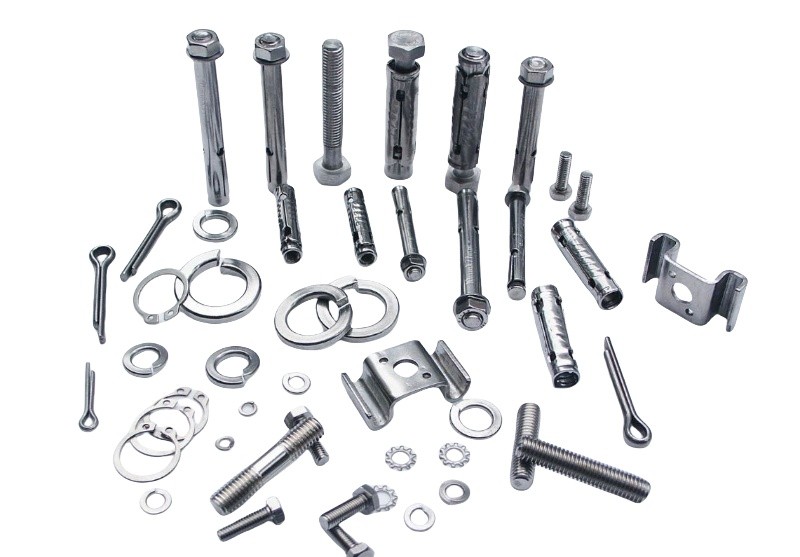